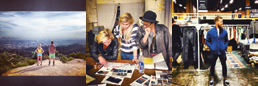
When Robert Lohman, environmental studies degree in hand, decided to enter the apparel manufacturing business, he had two goals. “We wanted to come up with a basics brand that was all organic,” he says, “and we wanted it to be made in Los Angeles.” That was back in 2010, and conventional wisdom would have dictated that someone with no industry background or training, going 100 percent organic with recycled material, and locating his manufacturing base in the heart of the Los Angeles garment district, would likely be out of business by 2011.

Conventional wisdom, in this case, would be dead wrong. Today, Lohman is CEO of the Groceries brand of men’s and women’s organic and recycled material tops. It can be found in over 400 stores worldwide, including Kitson and Planet Blue in Los Angeles and Barney’s New York and Opening Ceremony in Tokyo.
Groceries boasts annual sales in the seven figures, a 33,000-square-foot manufacturing facility downtown at the corner of Alameda and 7th, and 64 full-time employees. In addition to its own label, Groceries also sells volume private-label blanks to big names such as Paul Mitchell and Pearl Jam. The company is doubling its size every nine months. In other words, Groceries is a rousing success.
What accounts for it? To begin with, a strong corporate vision combined with a healthy dose of stubbornness. “We’d rather go out of business than manufacture nonorganic shirts and manufacture overseas,” Lohman says. “We will not go against our DNA that way.” And Lohman credits one other key component for Groceries’ achievements. “We really wouldn’t be here without Tukatech,” he says.
“Tukatech’s staff members were very cooperative during the installation process, and provided overall guidance and suggestions for our cutting room,” said Dinesh Virwani, Group Managing Director. “While our installation process is still continuing, we have already seen our pattern makers more than double the number of patterns they can produce in one day.”
Tukatech, a name well known and respected throughout the apparel industry, is the leading provider of fashion software and hardware technology solutions. The 18-year-old company, headed by industry veteran Ram Sareen, has built a devoted following among designers, manufacturers, and distributors worldwide, having sold some 19,000 systems and replacing over 5,000 competing systems in the process. Its advanced TUKAcad software is arguably the most instinctive and ultra-efficient 3D and 2D patternmaking, marking, and grading software on the market, while its SMARTmark module maximizes marker placement with surgical precision to make use of every usable square inch of fabric. Its advantages over its “very expensive and rigid” competitors are many, Lohman says, but for him two qualities were critical: TUKAcad is instinctive and easy to use with built-in videos and self-training audio help and support for every function, and Tukatech’s prices are affordable and terms flexible. Tukatech “allowed me to rent for $200 a month, which made so much sense to me since we were getting started from nowhere,” he explains. “We didn’t purchase any hardware, like plotters or digitizers, because we could use TUKAcenters. Suddenly, we had the same powerful tools big apparel companies used. That was empowering.”
Those advantages were key, Lohman goes on, because of Groceries’ ambitious, locally based, vertical-integration business model. “A lot of brands outsource their manufacturing, especially overseas,” he says. “We think you can be more profitable manufacturing in the U.S., and it reduces your carbon footprint.”
Still, the challenges are many. “We take on all the headaches that come with manufacturing here because we gain speed, the ability to react to trends, and also to manufacture at a lower cost,” Lohman says. The company also takes a smaller margin to be able to compete with nonorganics. “We focused on price point because we want to compete not only with other organic companies but with nonorganics as well. Since there’s no middle man, we pass that savings on to the buyer. If we didn’t manufacture here, we wouldn’t be able to offer this kind of pricing and have the success we’ve had in the market.”
Renting TUKAcad “gave us an efficiency as far as saving fabric, but, more than anything, it allowed us to work on our own timeline, even all night if we wanted to,” Lohman says. He has since bought the software, and, three months ago, he added the SMARTmark module. “It’s been another transformation in our company,” Lohman continues. “SMARTmark is TUKAcad on steroids. It is really and truly amazing.” What used to take 30 to 40 hours per week now takes “less than two hours.” Expecting a 5 percent fabric savings, SMARTmark is realizing near 20 percent, which should save Groceries an estimated 100,000 yards of fabric next year. “Efficiency is a huge part of being an eco company,” Lohman says. “We save money, use fewer resources, and create more demand for organic fabrics.” And that fits Groceries’ corporate goals to a T.
Lohman also credits Groceries’ success to “immense help” from Sareen and Tukatech’s strong customer support. “We made good business decisions manufacturing here it’s not just a gimmick,” Lohman says. “But I’m not sure we’d be able to exist without Tukatech. We couldn’t compete with much larger companies, wouldn’t have the flexibility to produce and design. It’s very empowering for a small company to have that much strength in that type of software. Those are the words flexibility and empowerment that are the keys to our success.”